123 1960 年,表面贴装技术开始发展。20 世纪 80 年代,表面贴装技术得到广泛应用。到 1990 年,许多高端印刷电路板组件都采用了表面贴装技术。传统的电子元件经过重新设计,直接附着在电路板表面的金属片或端盖上。简单地说,表面贴装技术是电子组装的一部分。SMT 制造负责将电子元件安装到 PCB 表面。以这种方式安装的电子元件称为表面贴装器件(SMD)。这取代了通常需要通过钻孔布线的方式。
与通孔安装相比,SMT 的电子元件更小。这也意味着它能更频繁地在电路板的两面贴装元件。如今,由于表面贴装技术在印刷电路板制造工艺中的诸多优势,几乎所有商业制造的设备都使用表面贴装技术。由于表面贴装技术在印刷电路板制造过程中具有诸多优势,因此它能最大限度地降低制造成本,同时有效利用印刷电路板空间。本文将讨论表面贴装技术的各种优势。

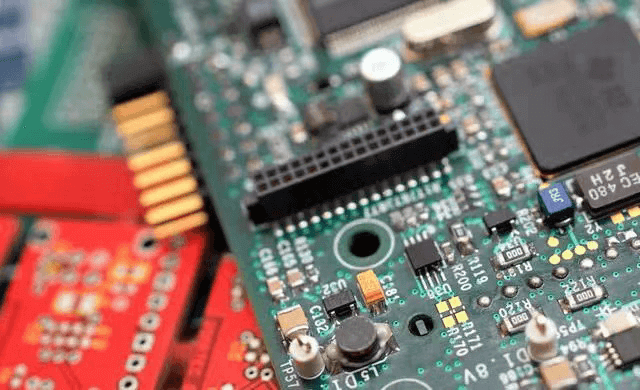
体积小、重量轻
表面贴装技术(SMT)允许元件更靠近电路板。这样就可以设计出更小的印刷电路板。这意味着组装设备可以设计得更轻、更紧凑。
在正常情况下,SMD 元件比通孔元件小 60-80%。有些元件的尺寸和体积甚至可以减小到 90%。因此,贴片电子元件的尺寸和体积远远小于通孔插补元件。众所周知,SMD 元件体积小,重量轻。因此,它们在 SMT 印刷电路板上占用的空间更少,从而使其更小更薄。
SMT 制造的零件通常不需要插入和焊接,因此通常比 PTH 零件小。SMT 元件不需要长引线,这意味着设计人员可以在更小的空间内安装更多元件。这样就可以在电路板上使用 PTH 零件来完成。由于尺寸和体积小,SMT 零件通常比 PTH 零件便宜。SMT 零件也比 PTH 零件更容易获得。
低成本
与通孔式生产方式相比,SMT 生产方式的批量生产速度更快,因为它不需要在电路板上钻孔进行组装。这也意味着 SMT 制造的初始成本更低。SMT 电路板尺寸较小,不需要任何电镀通孔。许多 SMD 元件的成本也低于通孔电子元件。这有助于降低 SMT 电路板的制造成本。
由于表面贴装组件更小、更薄,SMT 生产过程中的包装和运输成本也随之降低。以前的电路板组装需要将通孔电子元件的引线手动插入电镀通孔中。而 SMT 制造则不同。在 SMT 生产中使用自动 SMT 贴片机后,它们可以自动贴在电路板上。这就降低了 SMT 制造的加工和生产成本。
由于封装紧凑、引线电感较低,SMT 制造的辐射环面积较小。因此,它具有更好的 EMC 兼容性(更低的辐射发射)。在 SMT 制造过程中,元件引线无需弯曲、成型或剪短。这缩短了 SMT 制造的整个流程,提高了生产率。经验表明,相同功能电路的加工成本低于通孔插补,总生产成本一般可降低 30% 至 50%。
表面贴装技术
采用 SMT 工艺制造的印刷电路板更加紧凑,电路速度也更快。随着电子设备对速度的要求越来越高,SMT 制造工艺越来越受到制造商的青睐。其高端元件可实现多任务处理。
元件可放置在电路板的两侧,并可连接更多元件。熔融焊料的表面张力会将元件拉到与焊盘对齐的位置,并自动纠正元件放置中的微小误差。
SMT 制造工艺可确保连接处的低电阻和低电感。这可减少射频信号的有害影响,并提供更好、更可预测的高频性能。
高度自动化
大多数 SMT 零件都可以使用自动取放设备方便地安装到电路板上。无源元件等大量零件从卷轴装入贴片机,而其他零件则从管式送料器或托盘装入。这是与 PTH 零件非常重要的区别,后者通常必须手动装配。由于尺寸和体积的原因,SMT 零件通常比 PTH 零件便宜。由于需求量大,SMT 零件也比 PTH 零件更容易获得。SMD 元件焊接条件的标准化、系列化和一致性使 SMT 高度自动化。由焊接过程引起的元件故障将大大减少,并将提高可靠性。
低噪音
SMT 印刷电路板组装可支持高密度,主要是双面印刷电路板和多层印刷电路板。由于延迟时间短,这些电路板能够进行高速信号传输。同时,由于 SMD 元件没有引线或引线较短,因此可减少射频干扰。此外,SMT 印刷电路板组件的抗振性更强,噪音更小。由于元件没有引线或短引线,电路的分布参数自然会降低,射频干扰也会减少。
实用且经济高效
如今,几乎所有商业制造的设备都使用表面贴装技术,因为这种技术在印刷电路板制造过程中具有许多优势。越来越多的 PCB 设备采用 SMD 或封装形式。这使得使用表面贴装技术进行制造变得非常实用和经济。
SMT 组装元件不仅结构紧凑,而且安全密度高。当印刷电路板双面粘贴时,组装密度可达每平方厘米 5.5 至 20 个焊点。由于电路短、延迟小,SMT 组装的印刷电路板可实现高速信号传输。同时,SMT 组装的印刷电路板具有更强的抗振性和抗冲击性。这对于实现电子设备的超高速运行非常重要。
MT 生产过程
SMT 制造通常由多个高度自动化的 SMT 制造流程组成,其中包括以下基本步骤。
木板材料:
焊盘(无孔)和焊膏是通过一种类似丝网印刷的工艺涂抹上去的。印刷电路板的位置由精确的模板控制,以确保只在需要的地方涂上材料。这最大限度地降低了成本。
- 自动元件拾取和贴片机。它能将所需的 SMD 和其他元件精确地定位在电路板上。这些元件通常通过卷轴或带子送入机器。在 SMT 生产中,集成电路等元件是在无静电介质中输送的。然后电路板进入焊接操作。SMT 制造将焊盘加热到所涂焊膏熔化并将元件粘合到电路板上的程度。
-
当印刷电路板的两面都使用元件时,在反面重复贴装/焊接过程。
- 印刷电路板上的任何热敏元件都可以在自动焊接后安装。无论是手动还是通过不会损坏元件的工艺。
- 然后对电路板进行 "清洗",以去除多余的助焊剂或焊接残留物。由于 SMT 制造过程中的贴装公差很小,这些残留物可能会导致元件短路。
- 产品完成清洗和干燥后,就可以进行最终质量检验了。检查的目的是查找可能造成潜在问题的元件缺失、对齐问题或焊接问题。有设备可以自动进行这些检查。
- 然后,对检查过的电路板进行必要的电路和功能测试。