Military PCB Assembly
When designing military PCBs. the manufacturing process of the boards is a little bit critical due to the ability invested to ensure that the circuit boards perform well and function reliably and efficiently. Yet, have you even for once noticed that those military PCBs with components solidly stuck on? Never think they are just there for decoration of a PCB board. An advanced circuit board will find it difficult to function well unless components are mounted on it. An assembled PCB has components installed on it
Design Guidelines for Military PCBs
- Press-fit components should be soldered
- Only military-grade components have a tolerance range between 1-2%
- The dielectric thickness inside the stack-up layout should be 3.5 mil minimum
- Software simulation programs are essential
- The prescribed width of the ring for the hole in military-grade PCB design is 7-8 mils minimum
- PCB routing should be taken care of at a 45° angle or less
- The layout design should focus on managing the maximum current demand of the circuit
- High-quality heat-resistant material must be used
PCB applications
Benefits of military PCB assembly
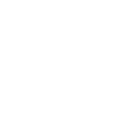
Use of Quality & high-performance raw material
Materials as high-temperature aluminum. copper and laminates are perfect materials to use in manufacturing PCBs.
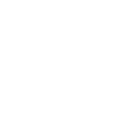
Standards for Military PCB /Military PCB standards
IPC-A-610E, MIL-PRF-31032, and ITAR are the recommended and major standards you should check for in every military PCB.
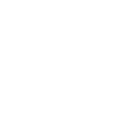
Resistance to environmental factors
Most of the released boards are synonymous with high temperature and humidity, tough environments, and tough and dust chemicals.
Applications of military PCB assembly
-
Power Distribution
- Auxiliary power units for radar control systems
- Communications systems
-
Defense navigation systems
-
Control tower systems
-
Unmanned vehicles
- Robotic systems
-
Jamming systems
-
Electronic countermeasures
-
Integrated Air Defense System
-
Underwater navigation systems
-
Security equipment