Rigid PCBs
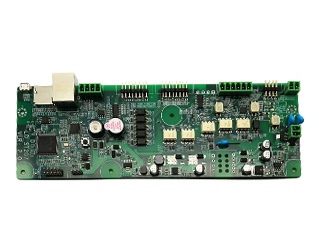
What Is Rigid PCBs?
Rigid PCB boards are conventional printed circuit board that is still popular in PCB manufacturing. This kind of printed circuit board has the largest number in the PCB industry. Generally speaking, the rigid PCB board is a single-sided printed circuit board and can be designed as a double-sided PCB board according to the special requirement of customers.
The commonest application of rigid PCB board is the computer motherboard that needs multi-layer rigid PCB board to distribute power and support communication between all components of the computer.
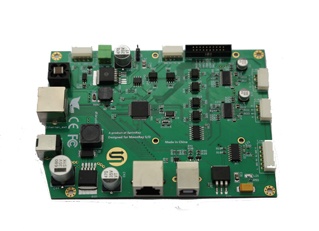
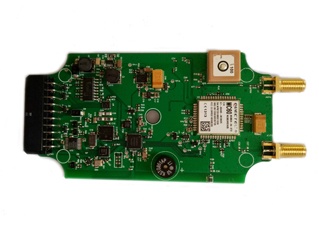

Application
Made by solid substrate material, the rigid printed circuit board is a kind of conventional printed circuit board that can’t be changed shape to suit narrow space while providing strength and rigidity to the printed circuit board.
Rigid PCB boards appear in our daily life as the component of GPS equipment, such as computers, tablets, mobile phones, and laptops. Excluding the electronics industry, rigid printed circuit boards are also used in important medical equipment, such as MRI system, CAT scans, and heart monitors. Additionally, the aerospace industry is also the applicable field of rigid PCB boards because they are made from copper and aluminium substrates that mean they will have a good performance in high-temperature environment.
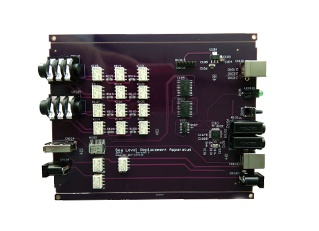
Rigid and flexible PCBs are very commonly used in the electronics industry to connect electronic components in different electronic equipment. The rigid printed circuit board is made of solid substrate material that prevents PCB board from distortion, while the flex printed circuit board is made of a flexible base and can be twisted, folded.
It seems like both rigid PCB board and flexible PCB board have the same basic purpose to ensure the electronic connection of the components on the board is normal, but considering differences between rigid and flex PCB board, PCB manufacturers must choose the right printed circuit board for their products.
Differences Between Rigid PCB Board and Flex PCB Board:
Conductive material: Rigid PCB board and flex PCB board have different conductive material. Rigid circuit boards use electro-deposited copper as its conductive material that supports circuit board structure but can not be folded. While flex PCB board can be used in certain narrow space because of its flexibility. Printed circuit board manufacturers use more flexible rolled annealed copper as its conductive material.
Manufacturing process: Compared with rigid PCB board, flex PCB manufacturers use overlay or coverlay instead of solder mask as the coat to protect the exposed circuit on a flex PCB board, because overlay is more flexible than solder mask and allows flex PCBs to be folded.
Cost: Usually flex PCB boards have a higher typically cost than rigid PCB boards because of its special design and flexible characteristic, but flex PCB boards can be folded for indirect saving.
Printed circuit board manufacturers use different layers to make up the rigid PCB board. Heat and adhesive process will join all layers together, and final provide the solid shape of the rigid printed circuit board.
There are 4 steps to build a rigid printed circuit board:
Step 1: Substrate layer manufacturing
The FR4, phenilces and epoxies are popular for rigid printed circuit board manufacturers as the substrate layer. Made of fiber glass, the FR4 is the commonest substrate materials, and provides stiffness and rigidity to the rigid board.
Step2: Copper layer laminating
With the help of heat and adhesive, rigid printed circuit board manufacturers add copper foil on the rigid PCB board. The standard rigid PCB board has copper layers laminated on both side.
Step3: Solder mask layer laminating
Rigid PCB board manufacturers add solder mask layer to protect the rigid circuit board from any damage in case of any conduction material touched with the copper layer.
Step4: Silkscreen layer laminating
Silkscreen layer aims to print logo or marks some symbol on the rigid circuit board. Rigid printed circuit board manufacturers provide white, grey, red black, and yellow colors for silkscreen layer.