Our Custom Rigid Flex PCBs Service

Rigid flex PCB design integrates elements from both hardboard and flexible circuit boards. It also features the advantages of both. Therefore, the rigid flex PCB can be folded or flexed while keeping the shape of areas that need extra support. The rigid flex board is typically multi-layered. So, it includes flexible circuit substrates joined with rigid boards. Rigid flex PCB manufacturers bury the flexible layers and penetrate the rigid sections of the PCB completely.
Advantages
- Resistance to high levels of shock and vibration
- Lightweight
- High circuit density
Choose Us for Your Rigid Flex PCB Project
We have an efficient PCB process and can complete your order in a short time. You can trust that we will provide you with the best service.
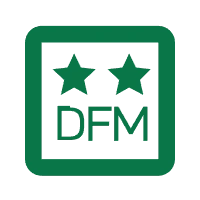
DFM free check service
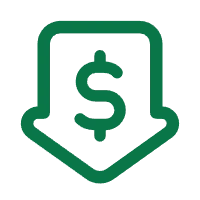
Give you the best factory price
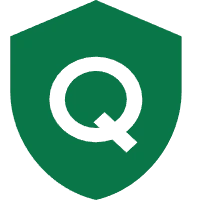
Strict quality inspection at every stage
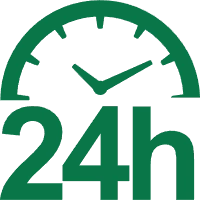
24-hour service
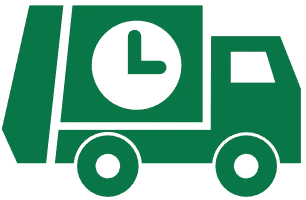
100% delivery on time
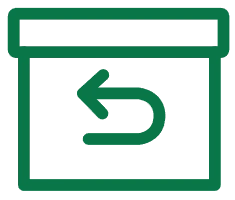
Return and refund service
Our Rigid-Flex PCBs Manufacturing Capabilities
Feature | Capability |
---|---|
Layer | 1-12 |
Min. Track/Spacing | 0.065 mm/0.065 mm |
Min. Hole/pa Size | 0.10/0.35 mm |
Rigid-Flex Thickness | 0.25-6.0mm |
Drilling accuracy | +/-0.05 mm |
PTH diameter tolerance | +/-0.05 mm |
MAX WPNL SIZE | 620 mm × 500 mm |
Finish Copper (Flex Part) | 0.5-2oz |
Finish Copper (Rigid Part) | 1-10 oz |
Surface treatment | ENIG |
Max board thickness: PTH diameter | 13:1 |
Build time | 7-20 days |
RFQ | 1-2 days |
Rigid Flex PCB Application
Rigid flex board is more expensive than other kinds of printed circuit board. However, its application has a wide range of industries. It is popular in the industry such as aerospace, medical devices, and the military. Besides, it is ideal for certain commercial products.
Rigid flex PCBs can be implemented in several circumstances as an optimal solution. This kind of printed circuit board used in this kind of situation can be seen as the most cost-effective choice.
- High-vibration and high-shock environment.
- Industries that need high-level reliability and precision more than cost considerations.
- High-density applications.
- Applications that need multiple rigid circuit boards.

How Are Rigid Flex PCBs Made?
There are four steps in the rigid flex PCB manufacturing process. It begins with the photochemical patterning of the circuit. And then, it involves the formation of microvia, adhesion, and clearing.
Step 1: Imaging pattern on rigid flex circuits is the primary process during the rigid flex PCB manufacturing process. The quality of images depends on the thickness of the light source and the resist. The manufacturers implement a collimated, intense light source to create a straight, clean image. Note that, thinner resist creates the finer image.
Step 2: The formation of microvia. This operation is a crucial process during the rigid flex PCB manufacturing process. A rigid flex PCB is different from the rigid one. However, manufacturers have a breakthrough in the control of the size and quality of drilled holes. The difference between rigid PCB and rigid board makes this process more difficult.
Step 3: A rigid flex board uses acrylic adhesive materials with a high thermal coefficient of expansion (TCE). It has low-flow and no-flow prepreg epoxies, which can reduce the adhesive tensility.
Step 4: The cleaning process is made after drilling to remove some smears that might cause low-reliability of rigid-flex PCB.

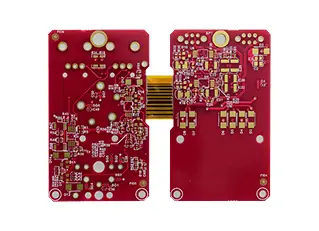
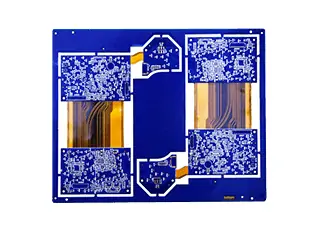
Advantages of Rigid Flex PCB
Rigid flex circuit boards are prevalent in a wide range of industries because of their special flexible design. Some popular advantages include:
- Reliability: Adding connectors on printed circuit boards might increase the risk of failure. Rigid-flex printed circuit boards can be regarded as a counterpart of the connector that will reduce the failure risk.
- Saving Space: Rigid flex boards have a special design that can be folded. As a result, it will reduce the use of space. The rigid flex board can save the space to install wire harnesses and high-profile connectors.
- Easy to Test: During manufacturing, the process implements an interconnection for all the subcircuits. As a result, rigid flex PCB manufacturers can test the rigid flex circuit board easily and quickly. Regular tests for rigid flex circuit boards can protect PCBs from some defects.
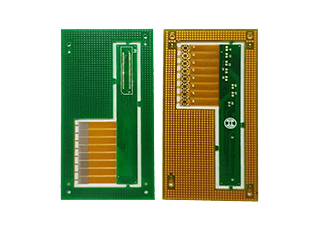
Rigid Flex PCB Cost

A rigid flex circuit board is popular because of the features of flexibility, reliability, and lower cost. As professional rigid flex PCB manufacturers, UETPCB will provide reasonable rigid flex PCB costs. We also highlight the factors that influence the cost of rigid flex circuit boards.
Generally speaking, the rigid flex PCB is more expensive than the equivalent rigid PCB. It is because of their materials and lower overall yields.
Flexible copper-clad laminates within the packaging are an important cost driver during manufacturing. Various materials can be implemented for PCB manufacturing. For example, polyester, polyimide, and PEN are noteworthy. Some of those are made from adhesive systems that can be bonded to the copper towards the circuit board, while others are not.
Rigid flex manufacturers usually use exclusively adhesive laminates with polyamide base materials. Note that these materials are more expensive. However, they improve the production and quality of the final product. Besides, they also need thicker polyimide films for controlled impedance designs. It ensures the normal function of the rigid flex circuit board.
The complex manufacturing process is another factor for rigid flex PCB cost. Rigid flex PCB manufacturers create rigid flex boards in separate components. They assemble them into the final board, which increases the cost of rigid flex PCB cost.
We’re Here To Help You
Any questions? Contact us anytime, and we’ll respond to your inquiries within 24 hours.