123In 1960 surface mount technology began to develop. Widely use surface mount technology in the 1980s. By 1990, you would use it in many high-end PCB assemblies. Traditional electronic components redesign to attach directly to a metal sheet or end cap on the surface of the board. Simply put, surface mount technology is part of the electronic assembly. SMT manufacturing is responsible for mounting the electronic components to the PCB surface. Electronic components mounted in this manner are called surface mount devices (SMD). This replaces the typical wires that need to rout through drilled holes.
Compared to through-hole mounting, SMT has smaller electronic components. This also means that it enables more frequent placement of components on both sides of the board. Today, almost all commercially manufactured devices use surface mount technology because of its many advantages in the PCB manufacturing process. Because it offers many advantages in the PCB manufacturing process, SMT minimizes manufacturing costs while making efficient use of PCB space. We will discuss the various benefits of surface mount technology in this article.

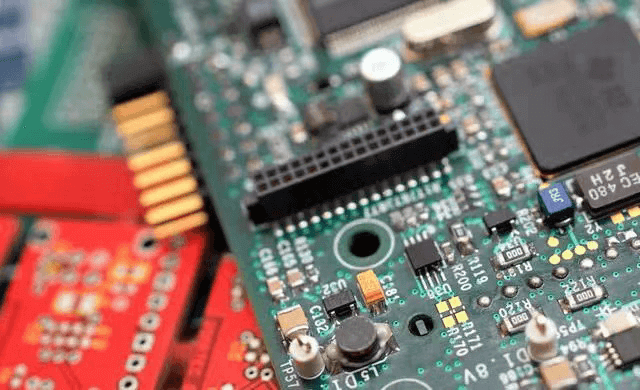
Small size and low weight
Surface mount technology (SMT) allows components to place closer to the board. This allows for the creation of smaller PCB designs. This means that assembled devices can design to be lighter and more compact.
Under normal circumstances, SMD components are 60-80% smaller than their through-hole counterparts. And can even reduce some components in size and volume by up to 90%. Therefore, the size and volume of SMT electronic components are much smaller than those of through-hole interpolation components. The small size of SMD components is well known, so it is also much lighter. As a result, they take up less space on the SMT PCB, which makes them smaller and thinner.
SMT manufactured parts usually do not require insertion and soldering, so it is usually smaller than PTH parts. SMT components do not require long leads, so this means that designers can fit more components into a smaller space. This can then be done on the board using PTH parts. And because of the size and volume, SMT parts are usually cheaper than PTH parts. SMT parts are also more readily available than PTH parts.
Low cost
SMT manufacturing allows for faster volume production than its through-hole counterpart because it does not require drilling the circuit board for assembly. This also means that the initial cost of SMT manufacturing is lower. SMT PCBs are smaller in size and do not require any plated through-hole. Many SMD components also cost less than through-hole electronic components. This helps reduce the cost of manufacturing SMT circuit boards.
Because surface mount assemblies are smaller and thinner, the cost of packaging and shipping aspects of the SMT manufacturing process are reduced. Previous circuit board assembly required the leads of through-hole electronic components to be manually inserted into plated through-holes. This is not the case with SMT manufacturing. With the use of automated SMT placement machines in SMT manufacturing, they can be placed on the board automatically. This reduces the processing and production costs of SMT manufacturing.
SMT manufacturing has a smaller radiation loop area due to its compact package and lower lead inductance. Therefore it has better EMC compatibility (lower radiated emissions). Component leads do not need to be bent, formed, or cut short for SMT manufacturing. This shortens the entire process of SMT manufacturing and increases productivity. Experience shows that the processing cost of the same functional circuit is lower than through-hole interpolation, which generally reduces the total production cost by 30% to 50%.
Surface Mount Technology
Printed circuit boards made using the SMT process are more compact, and the circuits are faster. With electronic devices now demanding speed, the SMT manufacturing process is becoming increasingly popular with manufacturers. And its high-end components allow for multitasking.
Components can place on both sides of the board and can connect more components. The surface tension of the molten solder pulls the components into alignment with the pads, and it automatically corrects small errors in component placement.
SMT manufacturing ensures low resistance and inductance at the connections. This reduces the harmful effects of RF signals and provides better, more predictable high frequency performance.
High level of automation
Most SMT parts can be easily mounted on the board using automatic pick-and-place equipment. Large quantities of parts, such as passive components, are loaded into the mounter from a spool, while other parts load from a tube feeder or tray. This is a very important difference from PTH parts, which typically must be assembly manually. SMT parts are typically cheaper than PTH parts due to their size and volume. SMT parts are also more readily available than PTH parts because they are in high demand. The standardization, serialization, and consistency of soldering conditions for SMD components make SMT highly automated. Component failures caused by the soldering process will be greatly reduced and will improve reliability.
Low noise level
SMT PCB Assembly can support high density, mainly double-sided PCBs and Multiplayer PCBs. Due to the short delay time, these boards are capable of high speed signal transmission. Also, because SMD components have no leads or short leads, RF interference is reduced. In addition, SMT PCB assemblies provide greater vibration immunity and are less noisy. Since the components have no leads or short leads, the distribution parameters of the circuit are naturally lower, and RF interference is reduced.
Practical and Cost-Effective
Today, almost all commercially manufactured devices use surface mount technology because it offers many advantages in the PCB manufacturing process. Increasingly, PCB devices are being offered in SMD or package form. This makes manufacturing with SMT very practical and cost effective.
SMT assembled components are not only compact but also have a high security density. When PCBs are pasted on both sides, the assembly density can reach 5.5 to 20 solder joints per sq. cm. SMT assembled PCBs can achieve high speed signal transmission due to short circuits and small delays. At the same time, SMT assembled PCBs are more resistant to vibration and shock. This is important for achieving ultra-high-speed operation of electronic devices.
Processes involved in MT manufacturing
SMT manufacturing typically consists of several highly automated SMT manufacturing processes that include the following basic steps.
Board material:
The pads (without holes) and solder paste are applied by a process similar to screen printing. The placement of the PCB is controlled by precise stencils to ensure that material is applied only where it is needed. This minimizes costs.
- Automatic component pick-up and placement machine. It positions the required SMD and other components precisely on the board. They are usually fed into the machine via reels or tapes. In SMT manufacturing for components such as integrated circuits are delivered in a static-free medium. The board then proceeds to the soldering operation. SMT manufacturing heats the pads to the point where the applied solder paste melts and bonds the components to the board.
-
Repeat the placement/soldering process for the reverse side when both sides of the printed circuit board are used for components.
- Any thermal component contained on the PCB can mount after automatic soldering. Either manually or through a process that does not damage the components.
- The board is then “cleaned” to remove excess flux or solder residue. These residues can cause component shorts due to the close placement tolerances in SMT manufacturing.
- Once the product can finish, cleaned, and dried, it is ready for final quality inspection. The inspection looks for missing components, alignment issues, or soldering problems that could create potential problems. There is equipment available to automate these checks.
- The inspected board is then subjected to any required circuit and functional tests.