What is aluminum PCB
Introduction to aluminum pcb board
Aluminum circuit board is the most common circuit board among metal PCBs. The aluminum substrate is a metal-based copper clad laminate with good heat dissipation function. Generally, a single panel is composed of a three-layer structure: a circuit layer (copper foil), an insulating layer, and a metal base layer. Because the aluminum PCB has a heat dissipation layer, it has a good heat dissipation function, which can effectively reduce the component’s operating temperature and extend the service life of the product.

The working principle of aluminum PCB
First, the surface mounts the power device on the circuit layer. The heat generated during the operation of the device will be quickly transferred to the metal base layer through the insulating layer. Then the metal base layer transfers the heat out to realize the heat dissipation of the device.

The structure of aluminum PCB board
- Copper foil layer: The copper layer used is thicker than standard copper-clad laminates. A thicker copper layer means greater current-carrying capacity.
- Dielectric layer: The dielectric layer is a thermally conductive layer with a thickness of about 50μm to 200μm. It has low thermal resistance, so it is suitable for its application.
- Aluminum substrate: The third layer is an aluminum substrate, which is made of aluminum substrate. It has a high thermal conductivity.
- Aluminum-based film: Aluminum-based film is optional. It has a protective effect by protecting the aluminum surface from scratches and unnecessary corrosion.
Advantages of aluminum PCB board
Compared with traditional FR-4, aluminum pcb board can minimize thermal resistance. Therefore, it has excellent thermal conductivity. Compared with thick-film ceramic circuits, its mechanical properties are excellent. In addition, aluminum pcb board has the following unique advantages:
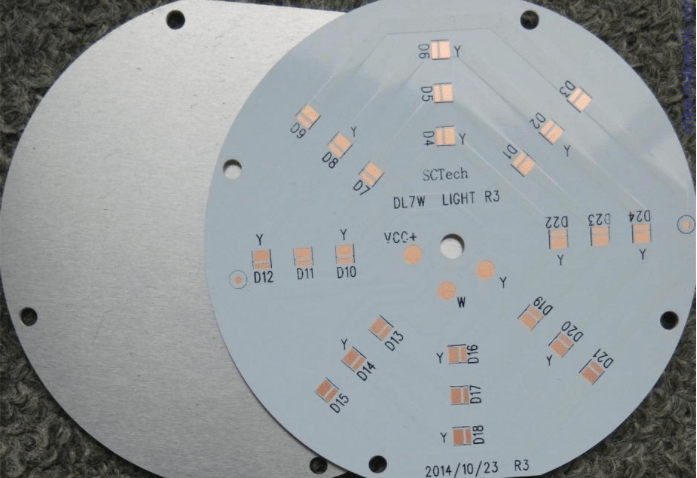
-
Heat dissipation
The heat dissipation capacity of PCB is much better than that of standard PCB.
-
Durability
PCB provides higher strength and durability. Compared with PCBs based on ceramics and glass fibers.
-
Convenience
It is lighter than standard PCB. The assembly process of PCB is more manageable than standard PCB.
-
Environmental protection
Aluminum pcb material is environmentally friendly. It is non-toxic and recyclable and will not cause any harmful effects on the environment.
-
Quality
Aluminum pcb material meets RoHs requirements; it is more suitable for the SMT process. The use of PCB can reduce the thermal expansion and shrinkage of PCB components.
-
Assembly cost
PCB reduces the assembly of heat sinks and other hardware (including thermal interface materials); reduces product volume. PCB can reduce hardware and assembly costs; optimize the combination of power circuits and control circuits.
Types of aluminum PCB
1. Flexible aluminum PCB
The flexible aluminum PCB dielectric is the latest development of insulating metal substrate materials. The flexible aluminum pcb material features ceramic filler and polyimide resin and provides higher electrical insulation, thermal conductivity, and flexibility. When use it with flexible aluminum materials (such as 5754), we can tilte and shape the PCB to eliminate expensive items such as cables, fixtures, and connectors. Although these flexible aluminum pcb materials are flexible, we can bent and remain them in place permanently. They are not suitable for applications that require frequent bending of the material.

2. Mixed aluminum PCB
Using hybrid aluminum PCBs, we can manage non-thermal materials and thermally fuse them to aluminum substrates. Generally, a two-layer or four-layer aluminum PCB made of straight FR-4 is used. Fusion of this layer and thermoelectric medium to the aluminum clad pcb substrate can dissolve heat, act as a heat shield and increase flexibility.
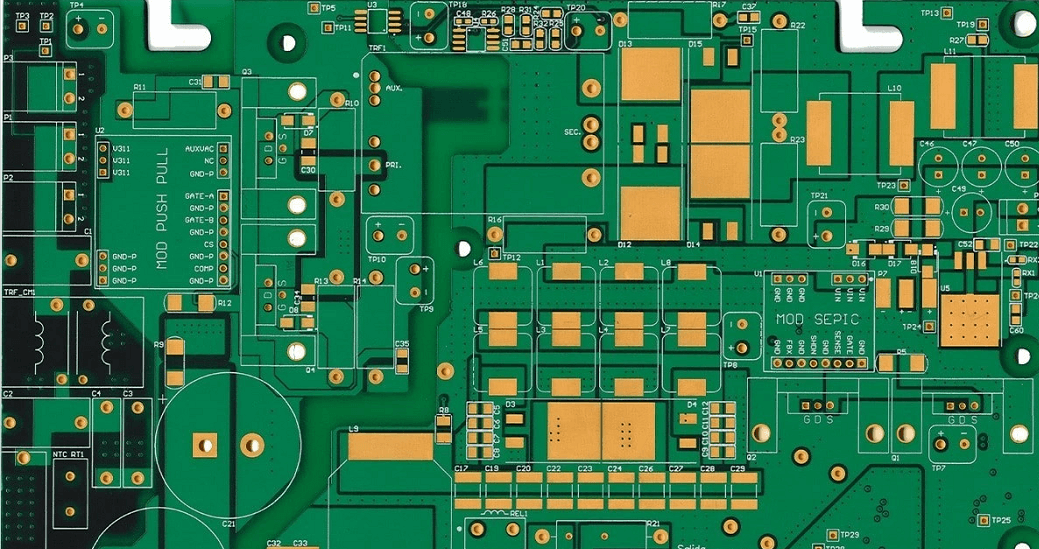
Other benefits of mixed aluminum PCB include:
- The hybrid aluminum PCB structure is cheaper than PCBs made of all thermally conductive materials.
- Mixed aluminum PCB eliminates related assembly steps and expensive heat sinks.
- We can use mixed aluminum PCB for RF applications. In these applications, PTFE surface laver can enhance the lost function
- Compared with standard FR-4 products, mixed aluminum PCB has better thermal performance
3. Through-Hole Aluminum PCB
In highly complex structures, a single layer of aluminum can form the central core of a multi-faceted thermal structure. In a through-hole aluminum PCB, drill the aluminum before the lamination process and then use a dielectric to backfill the hole. Next, laminating the thermally conductive material (or sub-assembly) to both sides of the PCB through a thermal adhesive material. After lamination, the components do drill like a PCB. Then plated through holes can pass through the gaps in the aluminum PCB to provide electrical insulation.

Classification of aluminum PCB copper-clad laminates
The main use of aluminum PCB

- Lighting products: high-power LED lighting products.
- Audio equipment: preamplifier, power amplifier, etc.
- Power equipment: DC/AC converters, rectifier bridges, solid-state relays, etc.
- Communication products: high-frequency amplifiers, filter appliances, and transmission circuits.
- Office automation equipment: motor drives, etc.
- Automobiles: electronic regulators, igniters, power controllers, etc.
- Computer: CPU board, floppy disk drive, power supply equipment, etc.
Difficulties in aluminium pcb manufacturing process
The aluminum pcb manufacturing process is basically the same. The main discussion here is the manufacturing process, difficulties, and solutions of PCB.
-
Copper etching:
The copper foil used for PCBs is relatively thick. However, if the copper foil exceeds 3 ounces, the etching requires width compensation. If it does not meet the design requirements, the trace width of the etched PCB will exceed the tolerance range. Therefore, we should accurately design the trace width compensation of PCB. The etching factor needs to be controlled during the manufacturing process.
-
Solder mask printing:
Due to the thick copper foil, the solder mask printing of aluminum PCB is complex. This is because if the trace copper of the PCB is too thick, the etched image will be very different between the trace surface and the substrate, and the solder mask printing will be difficult. Therefore, it is necessary to use two solder mask printing. The solder resists oil used should be of good quality. In some cases, the resin is filled first, and then the PCB solder resist is filled.
-
Mechanical manufacturing:
The mechanical manufacturing process involves mechanical drilling, forming, v-scores, etc. These processes are left in the internal vias, which tends to reduce the electric strength. Therefore, we should use electric milling cutters and professional milling cutters to produce them in small batches. And we should adjust the drilling parameters to prevent the PCB from producing burrs. This will help your machinery manufacturing.
why is aluminium used in circuit boards
Aluminum can divert heat away from critical components, thus minimizing the harmful effects, it may have on the board.
Aluminum has greater durability: Aluminum provides strength and durability to the product that ceramic or fiberglass bases cannot provide.
What materials are used on aluminum pcb insulation / prepreg
- Prepreg
- Laminate
- Aluminum foil
- Solder resist layers
Aluminum pcb vs FR4
The aluminum core PCB is the most common type of metal core PCB. Aluminum pcb vs fr4 is the more common type nowadays. So what is the difference between aluminum pcb vs fr4?
Price
FR-4 PCB is a very traditional board material. So his price is relatively low. Aluminum pcb vs fr4, compared to the aluminum substrate, is a little more expensive.
Thermal conductivity
Aluminum PCB has more excellent thermal conductivity than FR4. So in led lighting, manufacturers prefer aluminum pcb.
Applications
FR-4 PCBs use more widely than aluminum PCBs. Because FR-4 is not only a traditional material, but it is also inexpensive. Therefore it is preferred by manufacturers. Only industries that require high thermal performance will choose expensive aluminum substrates.
Key requirements when choosing an aluminum PCB manufacturer
All aluminum base pcb manufacturers follow the same aluminum pcb manufacturing process in most cases. The only real difference between aluminum based pcb manufacturers is the level of automation of their processes, the latest technology, and equipment.
-
Aluminum Circuit Boards
Several key items need to be considered if aluminum pcb manufacturers are to be able to produce any number of aluminum circuit boards, including efficiently
-
Specialized imaging equipment
Many aluminum backed PCBs does use for LED applications and are much longer than the production panels used in traditional aluminum pcb manufacturing process. Aluminum based pcb manufacturers must have custom 60″ wide UV imaging equipment or a device capable of screen printing images.
-
Specialized Scoring Equipment
The more common equipment available to obtain V-scores from traditional FR-4 materials is not suitable for managing aluminum PCBs. Aluminum base pcb manufacturers can help customers design the most cost-effective array to score panels whenever possible.
-
Punch presses larger than 40 tons.
For PCBs that are round or have unique features (slots, large holes, cutouts, etc.), you will need a aluminum pcb manufacturer that can punch out these features. Attempting to route aluminum base pcbs mechanically is costly to accomplish these features in a production environment.
-
In-line High Voltage Testing
A unique requirement of PCBs is that customers want to know if the product they are getting has passed a voltage test. Electrical test setups include withstanding voltage testing, which greatly reduces the cost to the customer.
UETPCB: experienced aluminum pcb manufacturer
UETPCB, one of China’s largest and most popular aluminum pcb manufacturers, occupies more than 3,000 square meters and specializes in manufacturing high quality pcb at low prices. We help you get the highest quality pcb within your budget.