What is Metal Core PCB?
Metal core PCB, referred to as copper mcpcb, is composed of an insulation layer, metal core and metal copper foil composite into a metal material as the substrate radiator, led metal core pcb can be located in the middle or top and bottom of the board. Copper metal core pcb has excellent heat dissipation, high thermal conductivity, and better processing performance.
If your product needs to work in high-temperature environments for extended periods, metal core PCBs are a better choice than regular FR-4. The metal core pcb is designed to transfer heat from critical board components to less critical areas. Aluminum core and copper core are common materials for metal substrates, and aluminum core board is the most common one, widely used in the LED lighting field. Compared with aluminum core PCB, copper core PCB has better electrical characteristics and performance, but higher cost.
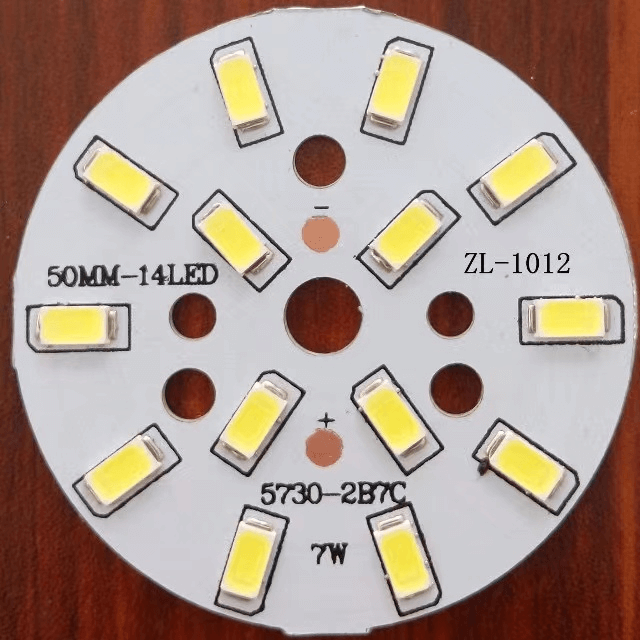
Metal Core PCB Applications:
Metal core pcbs that require much power usually generate much heat. And metal can quickly transfer heat by subtracting the heat from high-power components. So metal core printed circuit board do widely use in the following industries: power supplies, power converters, LED lighting systems, automotive systems, LED applications, photovoltaic systems.
What are The Advantages of Metal Core PCB?
1. Good heat dissipation
Metal core printed circuit board is a PCB with high thermal conductivity, and FR-4 PCBs have poor interlayer insulation. Metal core PCBs transfer heat eight to nine times faster than PCBs made of FR-4, they can avoid possible damage to the circuit or the components.
2. Better dimensional stability
With the change of environmental conditions, metal core PCB shows good dimensional stability. For example, when the aluminum substrate PCB is heated from 30°C to 150°C, the size of the PCB of the metal layer changes by 2.5-3%, which is very small.
3. Higher durability
Aluminum or metal core pcb boards offer higher strength and durability than FR-4, a common material used in PCB manufacturing. Greatly reduces the risk of accidental breakage during PCB manufacturing, assembly, or final product use.
4. Better lightweight
PCBs with metal core are lighter, last longer, and conduct electricity better than traditional FR-4 PCBs
Types of Metal Core PCBs:
1. Aluminum core PCB
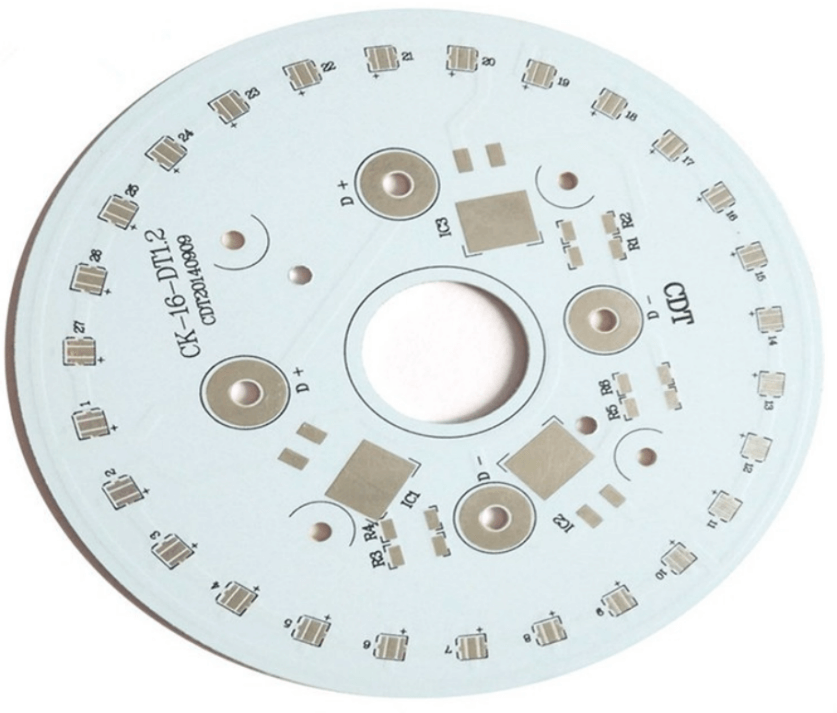
What is aluminum core PCB?
Aluminum core PCB is a kind of metal core pcb, with good heat dissipation performance. The common single-sided aluminium pcb board can compose of a copper layer, insulation layer, and aluminum base layer. At present, many products are usually designed for double-sided aluminium pcb boards, which are composed of the copper layer, insulation layer, aluminum base, insulation layer, and copper layer. Aluminum core PCBs are commonly used in LED lamps and lighting systems.
For the aluminum base PCBs, the power components are mounted on the circuit layer, during the device working, the heat is transmitted to the aluminum base through the insulation layer, and then the aluminum base quickly transmits the heat out because of the good heat dissipation, not only the circuit is protected, but also the equipment is protected.
Advantages of aluminum core boards(vs. FR-4)
- Better thermal conductivity
- The dielectric used for aluminum substrates is typically 5 to 10 times more thermally conductive than conventional FR-4, and is thinner
- Heat transfer index is more efficient than traditional FR-4 PCBs
- Can use a lower copper weight than IPC recommends
Applications of aluminium core pcbs
Aluminium core pcb is widely used in the below equipment:
- LED lighting: LED Display, street lighting, etc.
- Power supply: DC/AC converter, switch regulator, etc.
- Communication electronic: high-frequency amplifiers, filter appliances, etc.
- Office automation: motor drivers, etc.
- Automobile: electronic regulator, igniter, power controller, etc.
- Computer: CPU board, floppy disk drive, power supply devices, etc.
- Power module: converter, solid relay, rectifier bridge, etc.
- Audio: input, output amplifier, balance, audio, and power amplifier, etc.
2. Copper core PCB
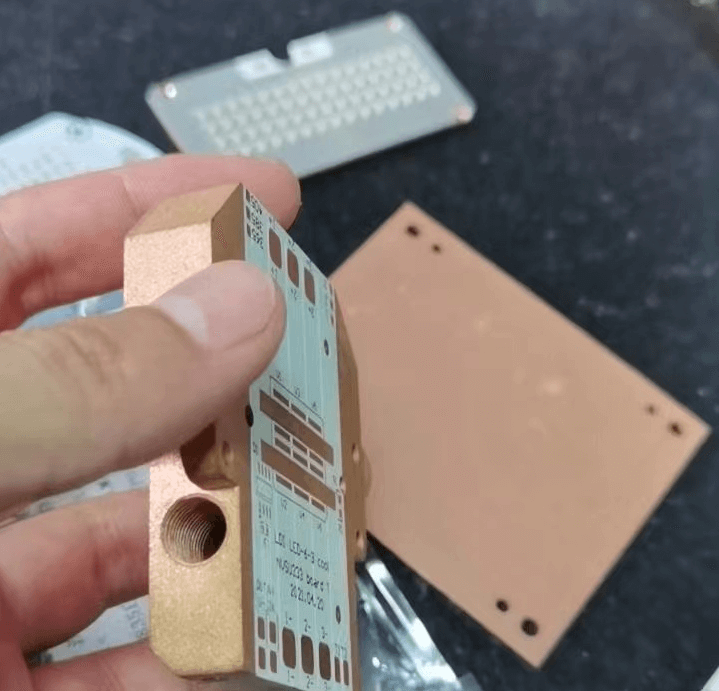
What is copper core PCB?
With the increase of copper metal core pcb component assembly density and integration, the signal transmission speed is accelerated, and the corresponding power consumption also increases. Especially in this era of 4 g networks lead, RF signal need excellent grounding performance, cooling requirements also will be improved at the same time, the performance of the common rigid PCB will not be able to meet its requirement, so a different kind of metal substrates, for that is the copper base PCB, the thermal insulation layer is copper substrate core technology, copper base PCB is one of the most expensive in the copper mcpcb. The thermal conductivity of copper mcpcb is many times better than aluminum or iron core. Copper substrate its circuit layer requires a large current-carrying capacity, so it needs to use a thicker copper foil, generally 35μm~280μm.
The overall structure of copper core PCB is very similar to that of aluminum core It has better thermal conductivity, electrical insulation performance, and machining performance. It is more suitable for high-frequency circuits, high heat dissipation devices, and precision communication equipment.
Advantages of copper core PCBs
High-thermal conductivity
The most important advantage of copper base PCB is the excellent high thermal conductivity, copper base PCB is the ideal choice for high heat components, because copper core can transfer heat quickly and efficiently, copper core substrate can work steadily for a long time, but also avoid damage to equipment.
Better electrical performance
Metal core pcbs have superior electrical performance, making these PCBs ideal for high frequency applications and precision communications equipment. Stable shape holding
Copper metal core pcbs retain their shape well, even under harsh conditions, without deforming, bending, or expanding due to high temperature or pressure stresses.
Better durability
Copper metal core pcbs have better mechanical strength and are more durable than aluminum and iron base PCB, resulting in longer PCB and component life.
Applicationsof copper core PCBs
- Solar energy converter
- Renewable energy
- High power rectifier
- The railway system
- Overload relay, power cord to monitor
Differencesbetween Aluminum PCB and Copper PCB
- The material price of the copper substrate is much higher than that of the aluminum substrate.
- The thermal conductivity of the copper core PCB is 2 times that of the aluminum core PCB: aluminum base: about 200 W/M.K. Copper base: about 400 W/M.K. Therefore, the heat dissipation of copper base is better than that of aluminum base.
- Single aluminum core PCB can not be directly drilledinto metallized, while the copper core PCB can be processed into metallized holes.
- Copper core PCB has a higher density per unit area, so it is heavier by weight than aluminum core PCB.
- Metal core pcb has higher ductility compared to aluminum core PCB.
- Compared with aluminum core PCB, copper core PCB has smaller shrinkage and warpage.