Chip on board is a process of mounting semiconductor chips in the surface of an insulating substrate. The chips are usually fabricated with multiple devices, and individual dies may be cut from a wafer before mounting them to the package. In this way, thinner substrates can be used which saves material cost, space, and weight.
What is chip on board led?
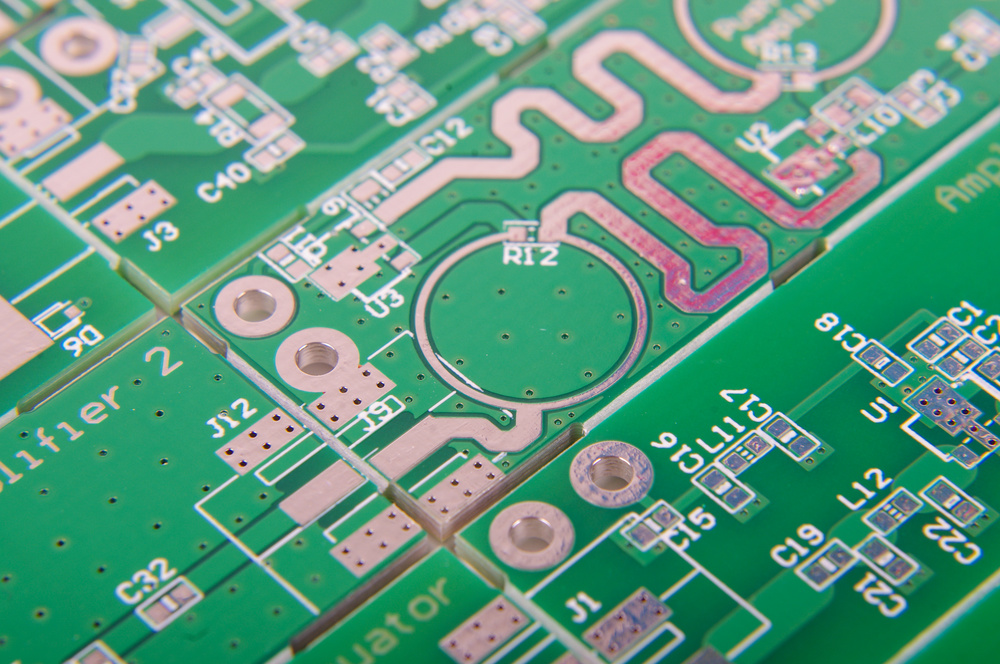
Chip on board, also known as Chip on board LED, is an assembly of LED chips bonded onto a base that acts as the heat sink. This technology can be used to incorporate LEDs into different packages that are easy to handle and install.
This type of lighting solution eliminates the need for using individual components like lenses or reflectors because they’re all integrated into one package.
The most common types of materials used for manufacturing these products are metal core printed circuit boards (MCPCB) and ceramic substrates since they have high heat-dissipating properties. However, other options such as plastics should be avoided in order to avoid poor thermal conductivity.
What is a chip on board LED technology?

A chip on board (COB) LED is a type of LED mounted on a lightweight and high thermal conductive substrate. These devices use chip-scale packaging which allows for much smaller light sources than traditional LEDs. The acronym COB for this technology was first coined by Cree, Inc., one of the major manufacturers of COB LEDs. The term describes how elements such as semiconductor die and wire bonds are mounted directly to an LED package without any additional components between them.
Similar to other types of packaged LEDs, chips onboard can be divided into different categories
History of chip on board
In semiconductor device fabrication, wafers undergo many processing steps to make integrated circuits (IC). During each step, some ICs will be defective due to impurities or other defects. Instead of discarding these still useful but non-defective die/wafers, they are sometimes diced into smaller pieces called dies or chips. These pieces can later be mounted onto a larger substrate or printed circuit board (PCB) to form an electronic assembly.
One of the earlier techniques used for mounting dies is wire bonding. Which involves attaching a small wire to connect two parts together. This method may be very effective. But if any one of the many wires attached fails. It will render the entire device useless. Later, develop an alternative technology called chip on board. The chip is mounted directly on the PCB using conductive adhesive. The interconnected dies and PCB substrate are then fused through reflow soldering or eutectic die attach. Chip on boards has several advantages over wire connections: lower cost and size. Second, higher reliability because there are fewer points of failure. However, the chip on board also has some disadvantages, such as low heat dissipation. Because most of the heat generated by the components is close to the chip.
Chips On Board vs Chip On Flex
The main difference between the two technologies is the substrate used. In COB devices, an individual die is usually mounted on a metal core printed circuit board or PCB (sometimes referred to as MCPCB). On the other hand, Chip on Flex (COF) devices uses an organic substrate that is flexible.
COB LEDs can provide better heat dissipation compared to regular surface mount LED technologies.
However, they also have some disadvantages. Using a metal core board to mount a semiconductor chip requires a more complex production process. The metal core board needs to be molded and laminated with chips. It can only mount on another material, such as plastic or metal. This becomes more expensive as the complexity requirements increase. Another disadvantage of this technology is that the output power density decreases due to increased thermal resistance between components.
Chip on board (COB) LED is a type of light-emitting diode. Which uses chip-scale packaging allowing it to be much smaller than traditional LEDs and has fewer connection points. These devices use lightweight and highly thermally conductive substrates. Unlike other surface mount technologies. Such as chip on board (Chip On Board) using metal core printed circuit boards or PCBs, and chip on flex using organic substrates. The acronym COB for this technology creates by Cree, one of the leading manufacturers of COB LEDs.
Advantages of chip on board LED vs. Surface Mount LED
1) Improved Quality of Light
One of the biggest advantages of using COB LED lighting is that it can provide a superior quality light compared to incandescent and fluorescent lighting options. In fact, COB lights can produce a crisp white light with very few distortions or color shading. In this sense, these LED lights are close to sunlight which contains all colors of the visible spectrum from infrared to ultraviolet wavelengths.
2) High Color Accuracy
Color accuracy refers to how closely the different colors produced by an LED match with their intended values. From this perspective, chip on board LED technology is among the best when it comes to general-purpose lighting. It’s good for use in office spaces and living rooms because of its ability to produce rich shades of white without significant color distortions.
3) Energy Efficiency
A typical incandescent bulb emits more than 90% of its total energy as heat instead of light. This is because the filament located inside the bulb has to be heated up to 2,550 degrees Celsius or 4,600 degrees Fahrenheit to emit light. On the other hand, LED lights only use 10-30% of their energy for producing light while 70-90% of it dissipates as heat. This means that chip on board LED technology requires less time and effort in order to produce the same amount of lumens compared with standard LEDs or CFLs.
4) Lower Operating Temperature
The lower operating temperature associated with COB LED lighting is another advantage since this eliminates the need for special cooling equipment. In this sense, the chip on board LED technology is a good option for environments with elevated temperatures such as attics or warehouses.
5) Greater Lumen Efficacy
A typical incandescent bulb has a lumen efficacy of approximately 12 lumens per watt while LED lights have a range of 50 to 100 lumens per watt. Moreover, if you use COB LEDs rather than regular LEDs, you can get up to 150 percent higher light output compared to CFLs and 30 percent more than traditional incandescent light bulbs.
6) Longer Life Span
COB LED lights have an estimated lifespan of between 40,000 and 50,000 hours depending on the manufacturer. This means that it can last even longer than most CFLs and halogen lights which typically only last up to 6,000 hours.
7) Energy Independence
A 100-watt equivalent COB LED light consumes less than 10 watts of power during operation. This makes it a cheaper option for homes and businesses even with rising energy costs. In fact, electric utilities in some regions offer rebates or discounts on COB lighting equipment that can further reduce electricity bills each month.
8) Environmentally Friendly
Compared with traditional incandescent bulbs, chip on board Led technology is not based on rare metals like mercury and argon gases. It doesn’t contain any toxic materials such as lead or beryllium either
9) Better Heat Dissipation
If you compare the heat dissipated by an incandescent bulb with that of COB LED lights, you will find out that there is a significant difference. In this sense, the technology used in COB LEDs allows it to easily disperse heat through its fins or pins compared with traditional lighting options which have metal filaments inside
10) Greater Brightness Level
Chip on board LED technology offers greater light output levels compared to other conventional LED lamps. If you use COB LED equipment rather than standard LED hardware, you can increase brightness levels without compromising energy efficiency.
11)Wide Application Range
Chip on board LED technology is more versatile compared with other forms of LED lighting. You can use it for many applications ranging from indoor lighting to outdoor illumination. It’s efficient enough to be used for almost any type of application without causing excess heat or significant losses in energy efficiency.
12) Eliminates the Need for Replacing Bulbs
Because COB LEDs are designed to operate at high temperatures. There is no need for replacing these light bulbs after some time, unlike CFLs which have a filament that gets burned out after a certain amount of time. Even if they’re still emitting light. As long as you buy them properly and place them under normal operating conditions. Chip on board lights should last between six months and three years depending on their rating and wattage.
13) Greater Design Flexibility
You can use COB LED lighting almost anywhere provided. It’s properly designed based on the application you’re using it for. This kind of technology is also compatible with many types of fixtures, optics, and lamp bases compared to standard LEDs which are only limited to a few options.
14) Easy to Use and Install
Due to their small size, COB lights can be installed into a variety of fixtures. This includes barebones candles, pendants, track lighting, wall packs, ceiling fixtures, and many others.
15) Compatibility with Many Applications
The chip on board LED light is compact and powerful. It is sufficient to replace traditional lighting solutions. Standard solutions are either too bulky or not bright enough. Therefore, these lights use in offices, warehouses, stadiums, shopping malls, parking lots and other places.
How are chip on boards made?
Can use the process known as wafer bonding to produce chips on boards.
Wafers of semiconductor material can obtain from a single crystal ingot.
These wafers are cut, cleaned, and polished to make them smooth, flat, and parallel. A thin layer is then deposited onto each of these surfaces to form the electrical connections required for the LED. This “sandwich” is then bonded with ultrasonic energy or a tack-and-bond approach, which can attach two surfaces without any adhesive materials being involved.
Once this procedure finishes, they can produce chips with all their electronic components by cutting out portions from the assembly. The most common method used at present starts off by sawing each of the wafers on both sides using a diamond-tipped blade. This process is complemented by cleaving, wire sawing, or plasma etching which are all used to remove specific areas.
The wafers separated into individual chips are then mounted onto an electrically conducting board material to complete the assembly. Each chip is typically pressed against this material using forces ranging between 1 ounce and 10 ounces. With COB LEDs, solder can use for electrical connections instead of wires. Because they allow for better thermal conductivity compared with traditional lighting technologies.
How to solder chip on board?

Step 1
Soldering chip on board is fairly simple. First, you should obtain the appropriate soldering equipment. This can include solder paste, soldering iron, flux, resin, and others depending on your preference.
You should prepare your work area to keep it as clean as possible. Follow the safety protocols provided by your manufacturer to avoid accidents during the process.

Step 2
Next, place the LED down on its substrate aligning them correctly with reference to the printed circuit board (PCB) or ceramic substrate. At this point, you can use heat transfer tape to help improve heat conductivity between both elements if needed.

Step 3
After that, all you need to do is apply some solder paste onto one of the pads of your chip on board light using a squeegee and then transfer it to your substrate.
Finally, you can solder the light by placing a small amount of solder onto the pad using a soldering iron. You should avoid using too much paste or applying too much heat because either situation can damage or crack the chips.
Conclusion
Chip on board Led technology is a simple and cost-effective way of integrating LEDs into different types of lighting fixtures. You can use this solution in a wide variety of applications ranging from area light sources, down-lights, backlight displays, signage to name but a few.
It offers many benefits such as the absence of complex optical systems such as lenses or reflectors which make them easier to manufacture. They also provide higher intensity levels compared with conventional alternatives since they produce more lumens per watt. Their Chip on board design allows for more efficient heat dissipation and lower degradation rates compared with other lighting solutions like OLEDs